Injection Molding stands out as a highly sought-after manufacturing technique, offering numerous advantages for businesses looking to optimize production processes. Firstly, its cost-effectiveness and high production efficiency attract companies aiming to enhance profitability. Moreover, the versatility of materials used in injection molding allows for innovative designs and complex shapes, ensuring that products meet precise specifications. As we delve deeper into this technique, we’ll uncover the reasons that make injection molding an essential choice in today’s competitive market.
Cost-Effectiveness of Injection Molding
Injection Molding stands out as a cost-effective manufacturing method for producing high-quality plastic parts. Here are several reasons why it is budget-friendly:
- Low Per-Unit Cost: Once the initial mold is created, the cost per unit significantly decreases, especially during large production runs.
- Minimal Waste: Injection Molding produces precise shapes and sizes, dramatically reducing material waste compared to other methods like machining, where excess material is often cut away.
- Shorter Production Cycle: The quick cycle times in Injection Molding lead to faster product turnover, allowing manufacturers to recoup their initial investment sooner.
Cost Comparison Table
Method | Initial Setup Cost | Production Time | Waste Percentage | Cost per Unit |
---|---|---|---|---|
Injection Molding | High | Very Short | Low (<5%) | Low |
Machining | Moderate | Moderate | High (up to 30%) | Moderate |
3D Printing | Low | Long | Moderate (15%) | High |
In summary, the cost-effectiveness of Injection Molding makes it an attractive choice for businesses aiming to optimize their manufacturing processes while maintaining quality and efficiency. Embracing this approach offers substantial savings in both time and money, ensuring a competitive edge in the market.
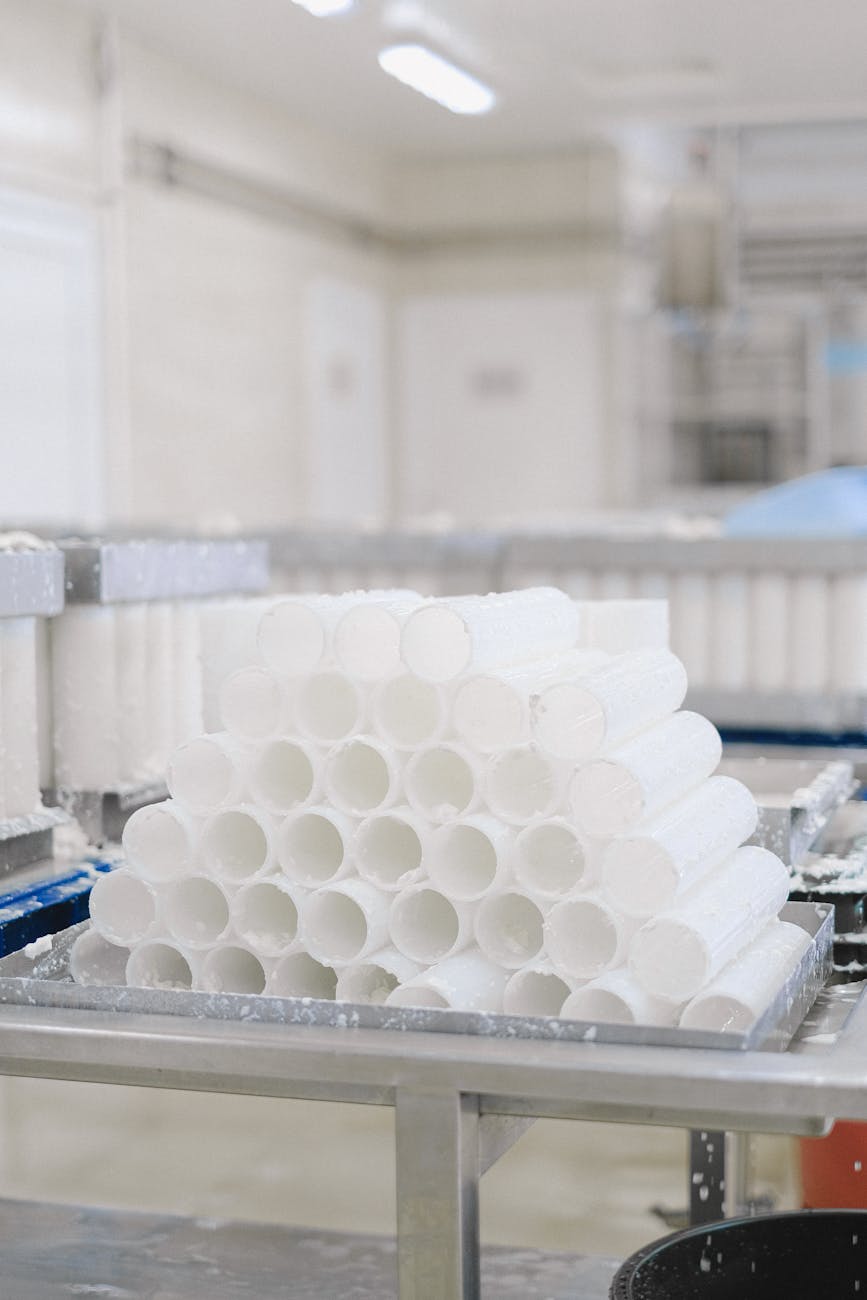
Photo by Anna Shvets
High Production Efficiency
Injection Molding stands out for its remarkable production efficiency, making it a favored choice among manufacturers. The technique enables the rapid creation of items with minimal delays. Here are some key reasons why Injection Molding excels in this area:
-
Short Cycle Times: The process can produce parts in mere seconds. This efficiency allows businesses to produce large quantities in a shorter timeframe.
-
Automation: Many Injection Molding processes are highly automated. Reduced human intervention minimizes the risk of errors, leading to consistent output.
-
Mass Production: Once the mold is created, Injection Molding allows for the rapid scaling of production. Manufacturers can easily transition from a small batch to large-scale production without significant adjustments.
-
Reduced Setup Time: Modern molds can be designed for quick-change, minimizing the downtime typically associated with switching production lines. This results in more running time and higher productivity.
Comparison of Production Methods
Method | Cycle Time | Setup Time | Automation Level | Cost Efficiency |
---|---|---|---|---|
Injection Molding | Seconds | Low | High | High |
Blow Molding | Minutes | Moderate | Moderate | Moderate |
3D Printing | Hours | High | Low | Variable |
CNC Machining | Minutes | High | Moderate | Low |
In summary, the high production efficiency of Injection Molding enables companies to meet market demands swiftly while optimizing resources, making it a smart choice for businesses looking to enhance their manufacturing processes.
Versatility of Materials
One of the standout features of Injection Molding is its impressive versatility in using a wide range of materials. This adaptability enables manufacturers to produce items tailored to specific needs and industries. Here’s why the versatility of materials in Injection Molding is crucial:
-
Thermoplastics: These are the most common materials used in Injection Molding. They become pliable when heated, allowing for various shapes and sizes. Examples include:
- Polypropylene (PP)
- Polyethylene (PE)
- Polyvinyl Chloride (PVC)
-
Thermosetting Plastics: Although less common than thermoplastics, these materials harden permanently after being molded. Notable examples include:
- Epoxies
- Polyurethanes
- Phenolic resins
-
Elastomers: These flexible materials offer excellent stretch and resilience. In Injection Molding, elastomers are used for:
- Seals
- Gaskets
- Soft-touch products
-
Engineering Plastics: These advanced materials provide superior strength and heat resistance, making them ideal for demanding applications. Common examples are:
- Nylon
- Polycarbonate (PC)
- Acrylonitrile Butadiene Styrene (ABS)
In summary, the versatility of materials in Injection Molding allows for innovation across industries. Whether it’s automotive, consumer goods, or medical devices, choosing the right material enhances product performance and meets market demands.
Precision and Accuracy in Manufacturing
Injection Molding stands out as a premier manufacturing process due to its remarkable precision and accuracy. This technique enables the production of intricate parts and components with minimal tolerances, which is crucial in various industries. Here’s how Injection Molding achieves this:
-
Tight Tolerances: Injection Molding can produce parts with tolerances as low as ±0.01 mm. This high level of precision means you can rely on consistently high-quality components.
-
Detailed Features: The process allows for the creation of complex geometries, including:
- Thin walls
- Fine details
- Textured surfaces
-
Repetition in Production: Once a mold is designed and tested, every subsequent part produced maintains the same accuracy, ensuring uniformity across large production runs.
-
Advanced Technology: Modern Injection Molding machines come equipped with computer controls that enhance accuracy. They monitor various parameters, preventing defects related to under- or over-injection of material.
In comparison to other manufacturing methods, such as CNC machining or 3D printing, Injection Molding provides unmatched precision for high-volume production. Below is a brief comparison:
Method | Precision Level | Production Speed | Cost-Effectiveness |
---|---|---|---|
Injection Molding | Very High | Fast | High for large runs |
CNC Machining | High | Moderate | Moderate to High |
3D Printing | Moderate | Slow | Low for small runs |
Overall, the precision offered by Injection Molding is vital for sustainable quality in manufacturing products, making it a preferred choice for applications demanding high accuracy.
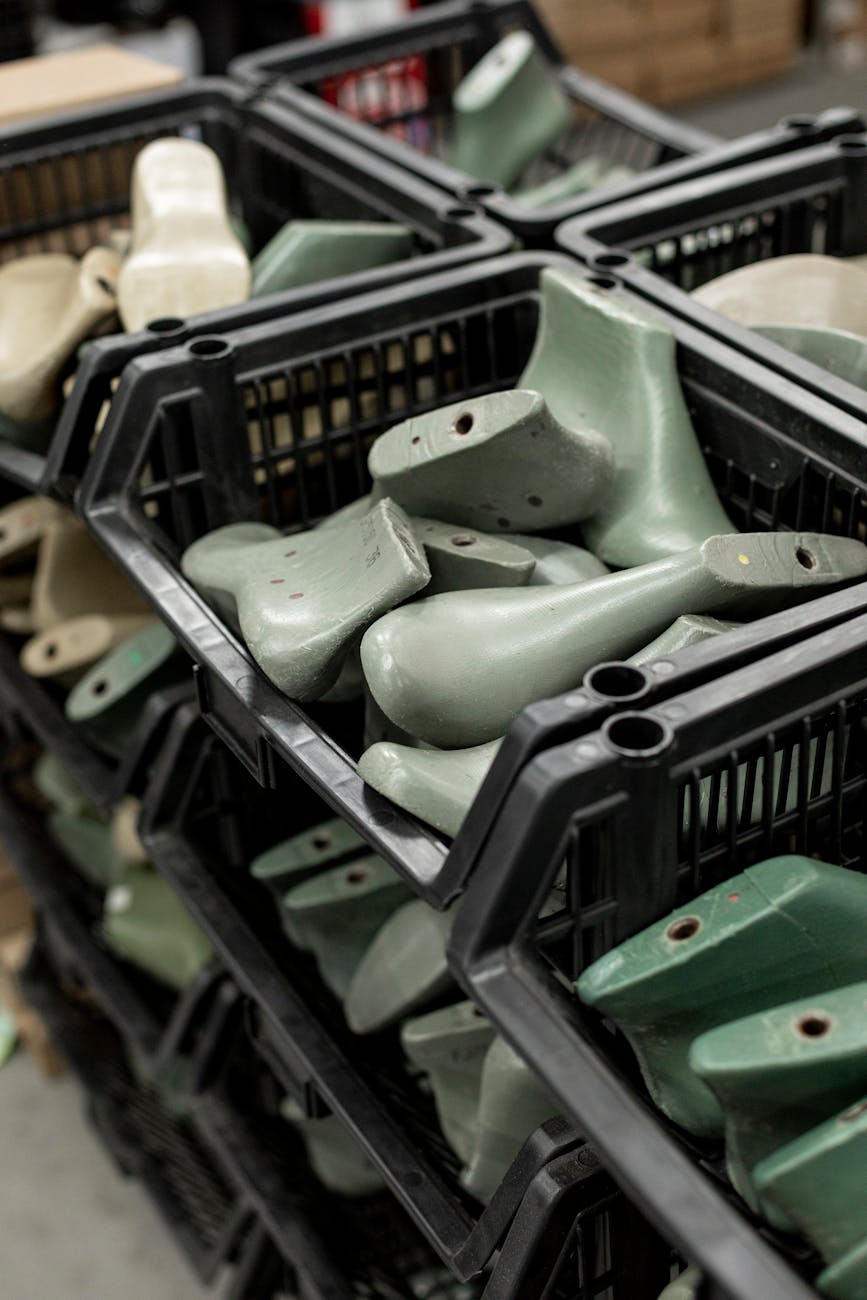
Photo by Fernanda Simões
Complex Shapes and Designs
Injection molding stands out as a superior manufacturing technique, particularly when it comes to producing complex shapes and intricate designs. Here’s why it’s essential for innovative product development:
-
Flexible Design Capabilities: Injection molding allows manufacturers to create parts with fine details, varying wall thicknesses, and elaborate geometries. This flexibility is not easily achieved with other manufacturing methods.
-
Tooling Precision: Custom molds used in injection molding can be designed to exploit every contour of your product. Advanced CAD/CAM systems produce molds that replicate even the most challenging designs accurately.
-
Multi-Material Integration: By utilizing co-injection molding, manufacturers can combine different materials into a single part. This amalgamation allows for enhanced functionality, aesthetics, and performance within a single product.
-
Prototyping and Iteration: Before full-scale production, injection molding enables quick and cost-effective prototyping. This process encourages experimentation with complex designs without excessive financial risks.
Comparison Table: Injection Molding vs. Other Methods
Feature | Injection Molding | CNC Machining | 3D Printing |
---|---|---|---|
Complexity of Design | High | Moderate | High |
Material Variety | Extensive | Limited | Limited |
Production Speed | Fast | Moderate | Slow |
Cost for Large Runs | Low | High | Moderate |
In summary, Injection molding not only supports innovative designs but also ensures that these designs can be manufactured efficiently and effectively. This capability lets businesses push the boundaries of creativity while maintaining cost-effectiveness.
Consistency in Product Quality
One of the standout benefits of Injection Molding is its ability to deliver exceptional consistency in product quality. This characteristic is vital for manufacturers aiming to meet strict industry standards and customer expectations. Here’s how Injection Molding achieves this remarkable consistency:
-
Precise Control:
- Advanced machinery allows for precise control over temperature and pressure during the molding process.
- This control ensures that each product maintains identical dimensions and properties.
-
Automated Production:
- Automation minimizes human error, leading to uniformity across multiple production cycles.
- Automated systems can replicate the same process without variation, ensuring every piece meets quality standards.
-
Material Uniformity:
- Injection Molding utilizes specific, homogeneous materials that yield consistent results.
- This uniformity not only enhances aesthetic appearance but also ensures durability and performance.
Aspect | Injection Molding | Traditional Methods |
---|---|---|
Control over Dimensions | High | Moderate |
Reproducibility | Excellent | Variable |
Production Cycle Variability | Low | High |
In summary, Injection Molding provides manufacturers with a reliable method to produce high-quality, consistent products. With tight tolerances and minimal variance, companies can trust that every item will meet their specifications, ultimately leading to higher customer satisfaction and reduced rejection rates.
Reduced Waste and Environmental Impact
One of the standout benefits of Injection Molding lies in its contribution to reduced waste and overall environmental impact. This technique not only maximizes the utility of raw materials but also promotes sustainability. Here are some key points highlighting how Injection Molding achieves this:
-
Material Efficiency: Injection molding utilizes a closed-loop system where excess plastic is regrinded and reused in subsequent production cycles.
-
Precision: The process ensures exact material dispensation, minimizing the chances of overstock and excess scrap materials. This leads to less waste compared to other manufacturing methods.
-
Shorter Production Cycle: With rapid production times, Injection Molding significantly reduces the energy consumption associated with manufacturing, as less time equates to less energy expended.
-
Reduced Emissions: High efficiency in production leads to fewer emissions from machinery, contributing positively to environmental goals.
Comparison of Waste in Different Manufacturing Processes
Manufacturing Method | Material Waste (%) | Energy Consumption |
---|---|---|
Injection Molding | 1-3% | Low |
CNC Machining | 10-30% | Medium |
3D Printing | 5-10% | Medium |
Traditional Handcrafted | 15-20% | High |
In summary, by adopting Injection Molding, manufacturers not only reduce waste but also take significant steps towards creating a more environmentally friendly production landscape. This makes Injection Molding an excellent choice for sustainable manufacturing practices.
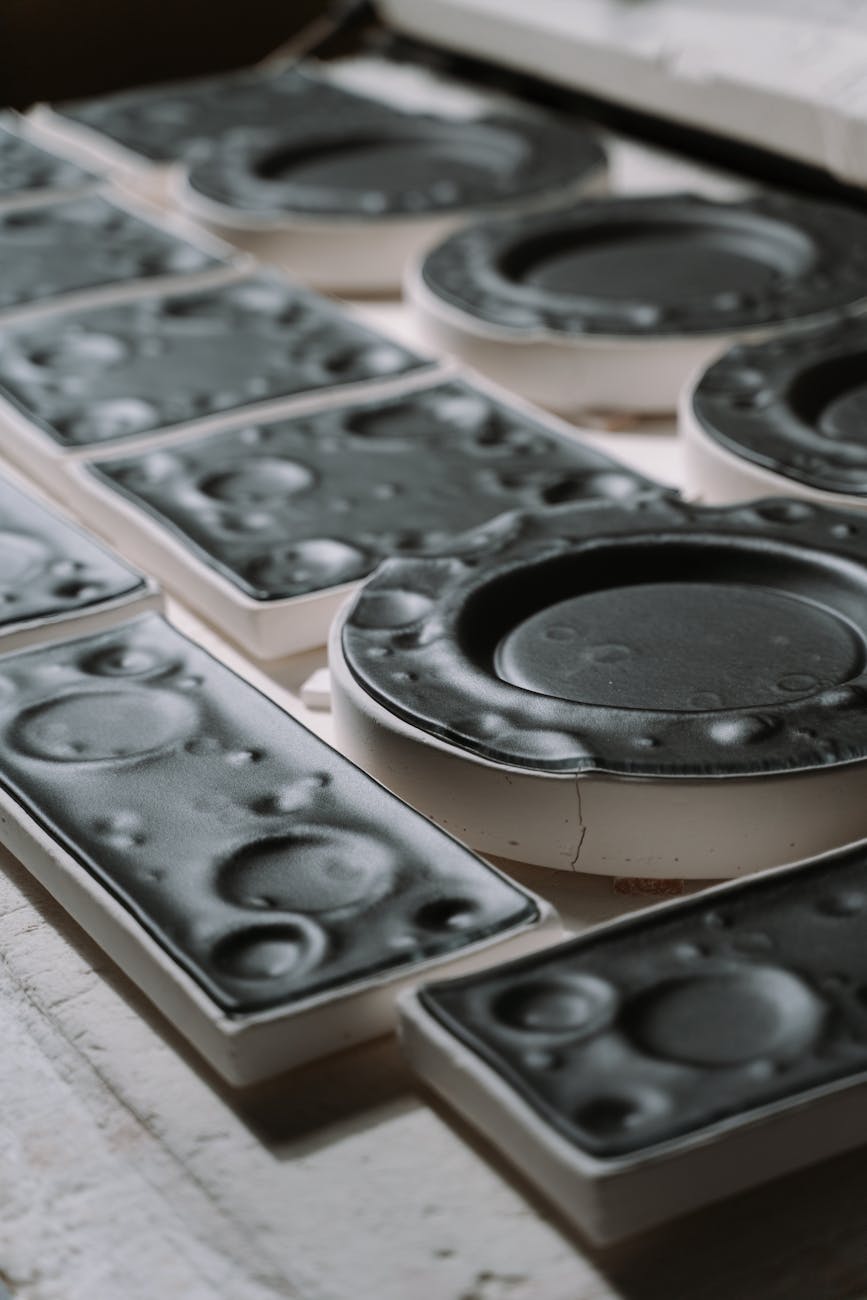
Photo by cottonbro studio
Faster Production Times
Injection Molding significantly improves production times compared to traditional manufacturing processes. Here’s how:
-
Rapid Cycle Times: The typical cycle time for injection molding ranges from 15 to 120 seconds, depending on part complexity. This efficiency means businesses can produce thousands of parts daily.
-
Automated Processes: High levels of automation in injection molding reduce labor costs and human error, ensuring that machines can run continuously with minimal supervision.
-
Speed of Setup: Modern injection molding machines require less time for changeovers between different products. With the right preparation, manufacturers can swiftly switch molds, enabling quick adaptation to market needs.
To highlight these benefits, consider the following comparison:
Process Type | Average Production Time per Part | Setup Time |
---|---|---|
Injection Molding | 15-120 seconds | Minimal (under an hour) |
Traditional Methods | Several minutes to hours | Extensive (several hours) |
Overall, injection molding enhances manufacturing speed while maintaining high quality. By minimizing production time, businesses can respond more rapidly to market demands and stay competitive.
Scalability for Large Production Runs
One of the standout advantages of Injection Molding lies in its scalability, making it an ideal choice for large production runs. As demand for products increases, businesses can leverage the capabilities of Injection Molding to effectively meet market requirements. Here’s how this technique supports scalability:
-
High Output Capacity: Injection molding machines are designed to produce high volumes of parts in a short time frame. This enables manufacturers to fulfill large orders efficiently.
-
Reduced Cycle Time: With fast cycle times, Injection Molding minimizes the time it takes to produce each item. This leads to higher output in less time compared to traditional manufacturing methods.
-
Automated Processes: Automation in Injection Molding not only boosts production speed but also ensures consistency across large runs. Automated systems reduce human error and streamline operations.
-
Cost Efficiency in Bulk Production: Scale economies come into play as production volumes increase. The more units produced, the lower the cost per part, making Injection Molding financially advantageous for large-scale operations.
Feature | Traditional Methods | Injection Molding |
---|---|---|
Production Speed | Slower | Rapid |
Initial Setup Cost | High | Moderate |
Cost Per Unit | Higher in large quantities | Lower in large quantities |
Flexibility in Design | Limited | Highly flexible |
In summary, Injection Molding offers unmatched scalability for businesses aiming for large production runs, ensuring efficiency, cost savings, and product consistency.
Applications of Injection Molding in Various Industries
Injection molding plays a crucial role across various sectors due to its adaptability and efficiency. Here are some key industries that benefit from this innovative manufacturing technique:
-
Automotive Industry: Injection molding is essential for producing complex components like dashboards, interior fittings, and engine parts. It allows for lightweight, durable materials that improve fuel efficiency.
-
Medical Sector: In the medical industry, precise and sterile components are critical. Injection molding produces items such as syringes, surgical instruments, and drug delivery systems with high levels of accuracy and consistency.
-
Consumer Goods: From toys to kitchenware, injection molding guarantees mass production of high-quality products. It enables manufacturers to create intricate designs with a variety of colors and finishes.
-
Electronics: This industry relies on injection molding for the production of housings, connectors, and components that need to meet strict tolerance and performance standards.
-
Packaging: Injection molding serves the packaging industry by producing lightweight yet robust containers and closures that ensure product safety and longevity.
Comparison of Industries
Industry | Key Benefits of Injection Molding |
---|---|
Automotive | Complex shapes, lightweight materials for fuel efficiency |
Medical | Precision, sterility, and consistency |
Consumer Goods | Mass production, intricate designs, color variety |
Electronics | High tolerance, consistent performance |
Packaging | Lightweight, robust, integrated designs |
Overall, the diverse applications of injection molding make it a fundamental technique across multiple industries, enhancing production quality and efficiency.
Frequently Asked Questions
What is the injection molding technique and how does it work?
Injection molding is a manufacturing process used to produce plastic parts by injecting molten material into a mold. The process begins with heating plastic pellets until they become liquid. This molten plastic is then injected under high pressure into a precisely designed mold cavity. Once the plastic cools and solidifies, the mold is opened, and the finished part is ejected. This technique is widely admired for its efficiency and ability to produce complex shapes with high precision.
What are the advantages of using injection molding for manufacturing?
Injection molding offers numerous advantages, including high production efficiency, consistent quality, and the ability to create intricate geometries. This technique enables manufacturers to produce large volumes of parts rapidly, reducing the overall time and labor costs. Additionally, injection molding allows for the use of various materials, including thermoplastics and thermosetting plastics, providing versatility. The process also minimizes material waste, making it a cost-effective option for mass production.
What industries typically use injection molding?
Injection molding is utilized across various industries including automotive, consumer goods, electronics, medical devices, and packaging. In the automotive sector, it is used for producing components like dashboards and interior fittings. For consumer goods, companies use injection molding to create items like toys and kitchen containers. The electronics industry relies on this technique to produce housings and components, while the medical field utilizes injection molding for devices and instruments that require precision and reliability.
What factors should be considered when choosing injection molding for a project?
When deciding to use injection molding for a project, several factors must be taken into account. These include the volume of production required, the complexity of the part design, the types of materials needed, and the budget for manufacturing. Additionally, it’s important to consider the lead times for the creation of molds and the production process itself. A well-thought-out design can significantly affect the efficiency and cost-effectiveness of injection molding.
Are there limitations to the injection molding technique?
Yes, while injection molding provides numerous benefits, it also has limitations. One significant drawback is the initial cost of creating molds, which can be expensive and time-consuming, particularly for complex designs. Additionally, injection molding is generally suited for high-volume production, making it less economical for small runs. The process may also require careful consideration of material selection, as some materials may not be suitable for injection molding due to their properties.